Our Services
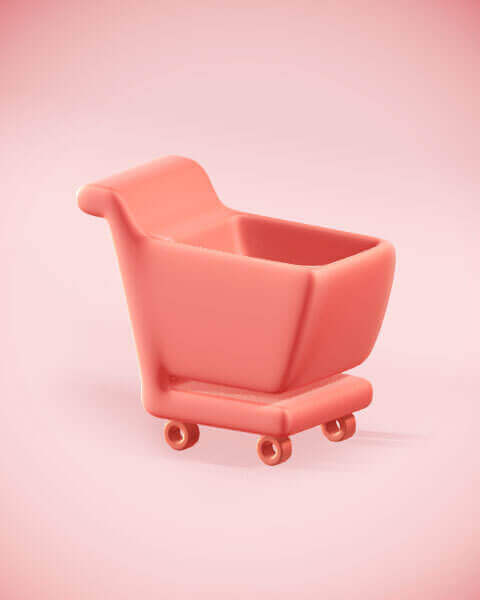
Free Quote
Whether you’re working on a small prototype or a large-scale production run, Desert Star Plastics is here to bring your ideas to life with precision, efficiency, and quality.
Request a Free Quote: Call us today at 602 340 1236 or fill out this form at Custom Product Display Quote for a no-obligation estimate. Our team of experts is ready to assist with your next plastic fabrication project.
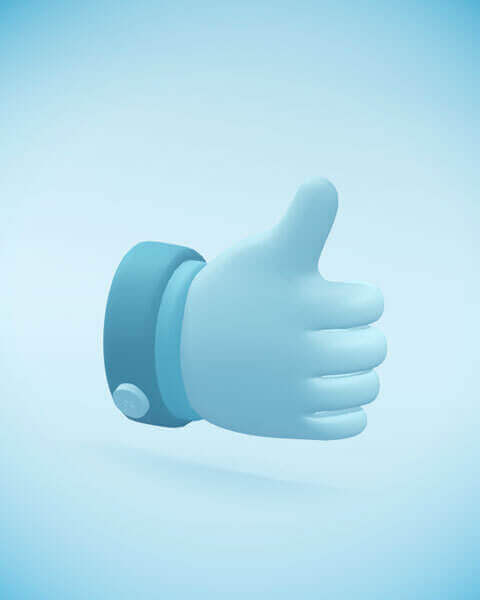
Adjusting the design

Plastic advises
help our customers to complete the production of their parts with the best quality and the correct price in mind.
Why Choose Us
Passionate
Desert Star Plastics is a leading plastic fabrication company based in Phoenix, Arizona. With years of experience and a commitment to excellence, we provide top-quality custom plastic solutions for industries ranging from Convenience store, fast food industry, manufacturing, construction to some weird stuffs. Whether you need parts, components, or full-scale assemblies, we specialize in delivering precise, durable, and cost-effective results tailored to your specific needs.
Professional
- Custom Plastic Fabrication: We offer tailored solutions for a wide range of industries, delivering the exact specifications you need.
- High-Quality Materials: We use only premium-grade plastics, ensuring strength, durability, and high performance.
- Advanced Technology: Our state-of-the-art equipment allows for precise cutting, welding, and forming of plastics, enabling us to handle even the most complex projects.
- Fast Turnaround: Need your plastic components fast? Desert Star Plastics works efficiently to meet tight deadlines without compromising quality.
- Local Phoenix Manufacturer: Proudly serving businesses in Phoenix, AZ, and surrounding areas with superior customer service and reliable delivery.
Support
As a local Phoenix-based plastic fabrication company, Desert Star Plastics is committed to delivering timely and cost-effective solutions. Our knowledge of the Arizona market helps us provide the best products for local businesses and industries, ensuring they get the most out of their plastic materials and products